PICKLING AND PASSIVATION OF STAINLESS-STEEL SURFACES
Stainless steels increase their resistance to corrosion thanks to the passive oxidized layer containing rich chromium on their surfaces. The passive layer on the surface can renew itself thanks to the supply of sufficient oxygen.
Removing the Shell Layer:
The shell is the dark gray visible layer on the surface. It is a process to clean the surface. It is done by the manufacturer before the material is shipped.
Pickling:
It is the process of removing a thin metal layer from the surface by using a mixture of nitric acid and sulfuric acid. The process aims to eliminate color changes around the weld seams.
There are three types of pickling methods:
- Immersion
- Spraying
- Circulation
Passivation:
Unlike the pickling process, no layer is removed from the surface in the passivation. Stainless steel is passivated itself under its structure, but in some cases, oxidative pickling may be required. The nitric acid used ensures the formation of a passive layer on the stainless surface.
Cleaning:
It is not possible to clean the dirt on the surface with the pickling process. For this, cleaning must be carried out following pickling and pacification.
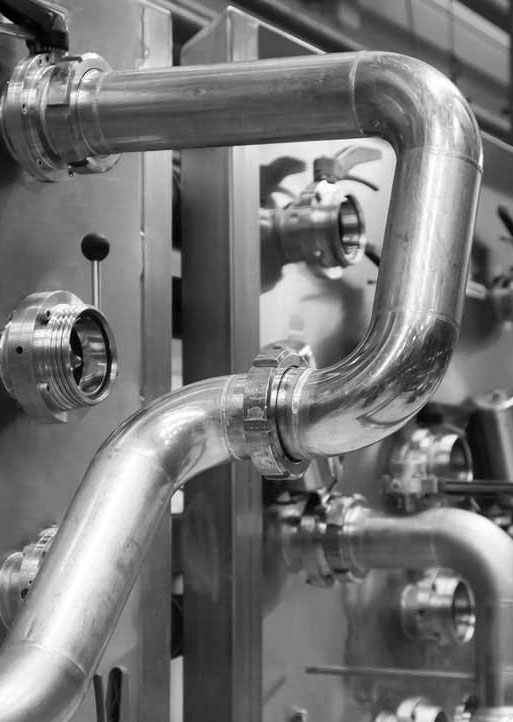
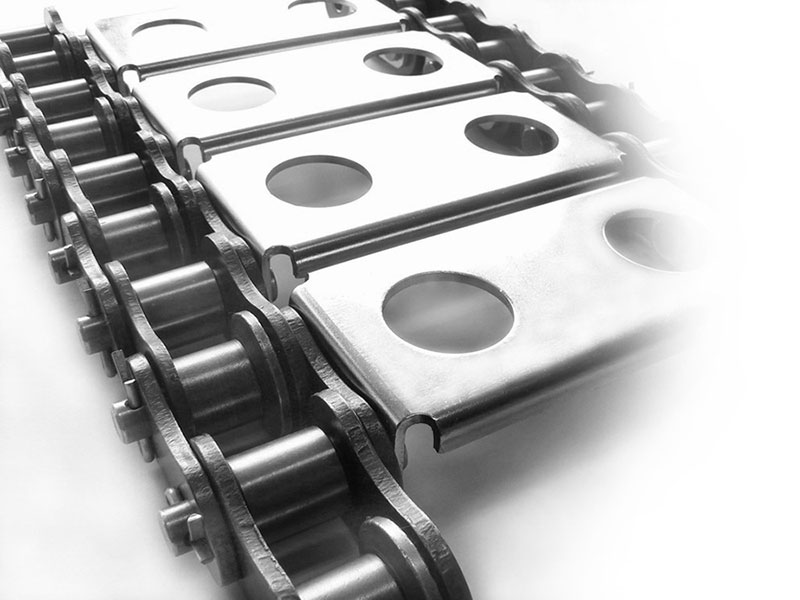
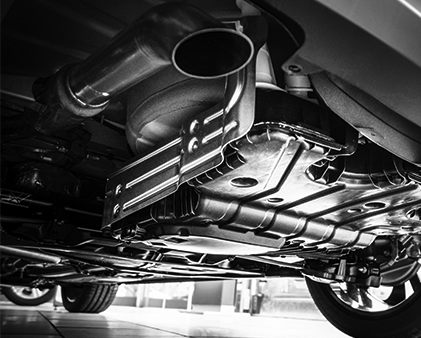
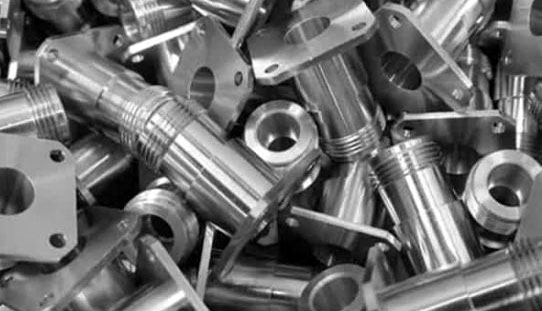
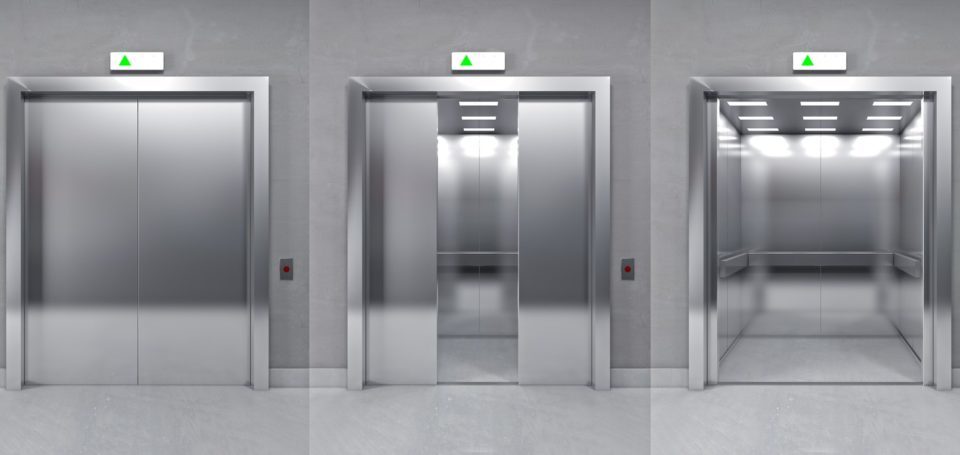
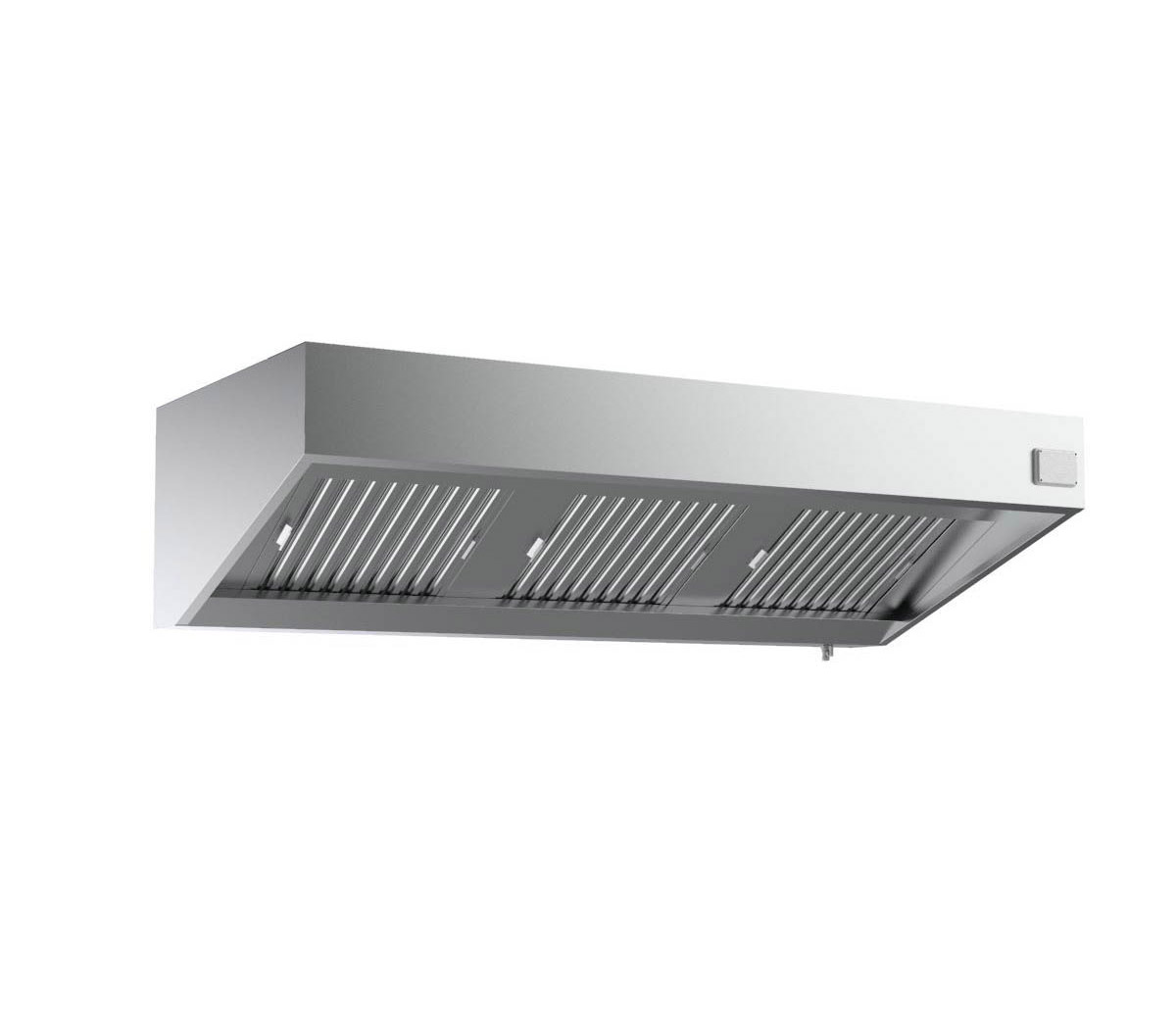
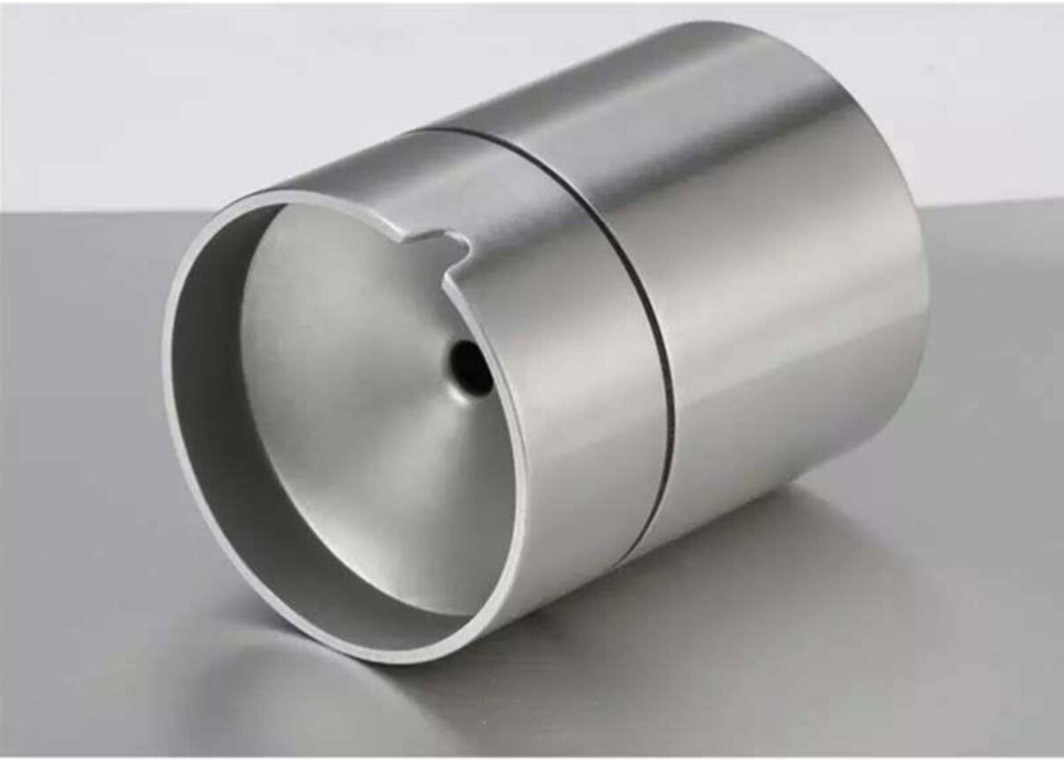
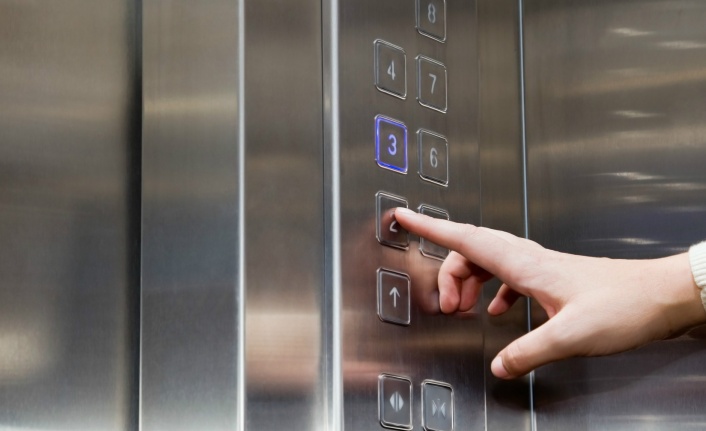
ELECTROPOLISHING ON STAINLESS STEELS
Electropolishing is the process of removing ions from the surface of a metallic object. It is a chemical surface finishing technique. The main purpose here is to minimize micro-roughness. The processes conducted for electropolishing are as follows:
- Pickling
- Passivation
- Acid cleaning
It is electropolishing (electro-polishing).
GRINDING AND POLISHING ON STAINLESS STEELS
These processes are conducted employing an interconnected bearing element containing hard particles. Grinding is the process of removing harmful surface materials such as weld grains and oxide layers. On the other hand, polishing is to give the surface brightness by removing a thin layer from the surface in the preparation of the surface for decoration.
POLISHING ON STAINLESS STEELS
Unlike grinding and polishing, the polishing process is not removing layers from the surface, but smoothing the surface, in other words, giving brightness.
SCRUBBING ON STAINLESS STEEL
It is an abrasive process like grinding and polishing. The difference between scrubbing and polishing is not removing layers from the surface, but giving the surface a different appearance. Softer abrasives and abrasives are used for scrubbing. A great variety of Scotch-Brite Band sanders, pads, or discs are used in the necessary auxiliary materials.
WELDING ON STAINLESS STEELS
Depending on the types of stainless steels, their suitability for welding is as follows;
Östenitik: Bu tür kaynak için en çok kullanılan türdür. Düşük oranda ferrit içerir, sıcak çatlamaya karşı hassas değildir, korozyona karşı dirençleri iyidir.
Ferritic: It is susceptible to corrosion, has sufficient ductility, and improved toughness.
Austenitic-Ferritic Duplex: They exhibit excellent toughness and ductility. They are not susceptible to hot cracking.
Martensitic: It has high tensile strength and hardness. Its toughness is at a good level.
DRAWING OF STAINLESS STEELS
In general, stainless steels have very good transformation properties. Therefore, it is used in many different fields. The most important transformation process in flat products is deep drawing. The drawing process is applied in two different ways as traditional and elongation.
In the traditional deep drawing process, the yield of the entire material is ensured with the female pulling ring of the stainless-steel part. In the drawing process in the form of elongation, the stainless-steel part is fixed to the holders in the die, and only the material thickness of the drawn part is thinned.
The use of grades with low yield strength and hardening rate is ideal in these processes. The recommended material for deep drawing is 304 DDQ.
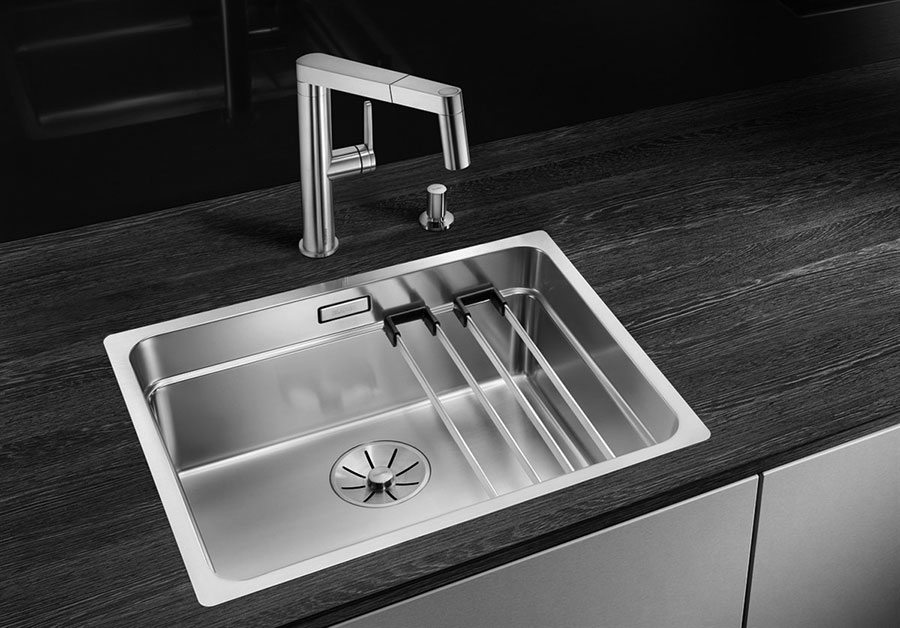
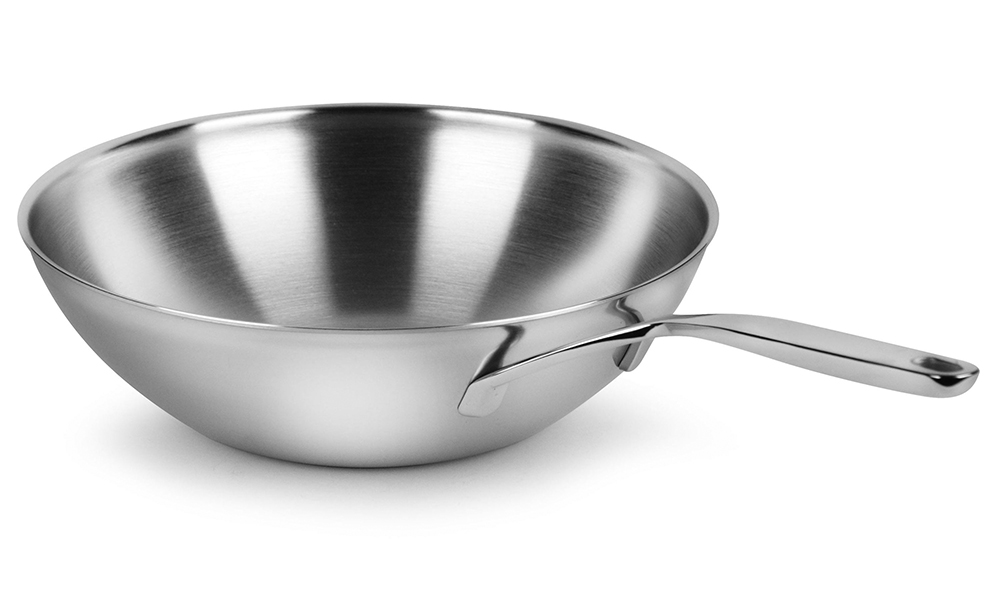
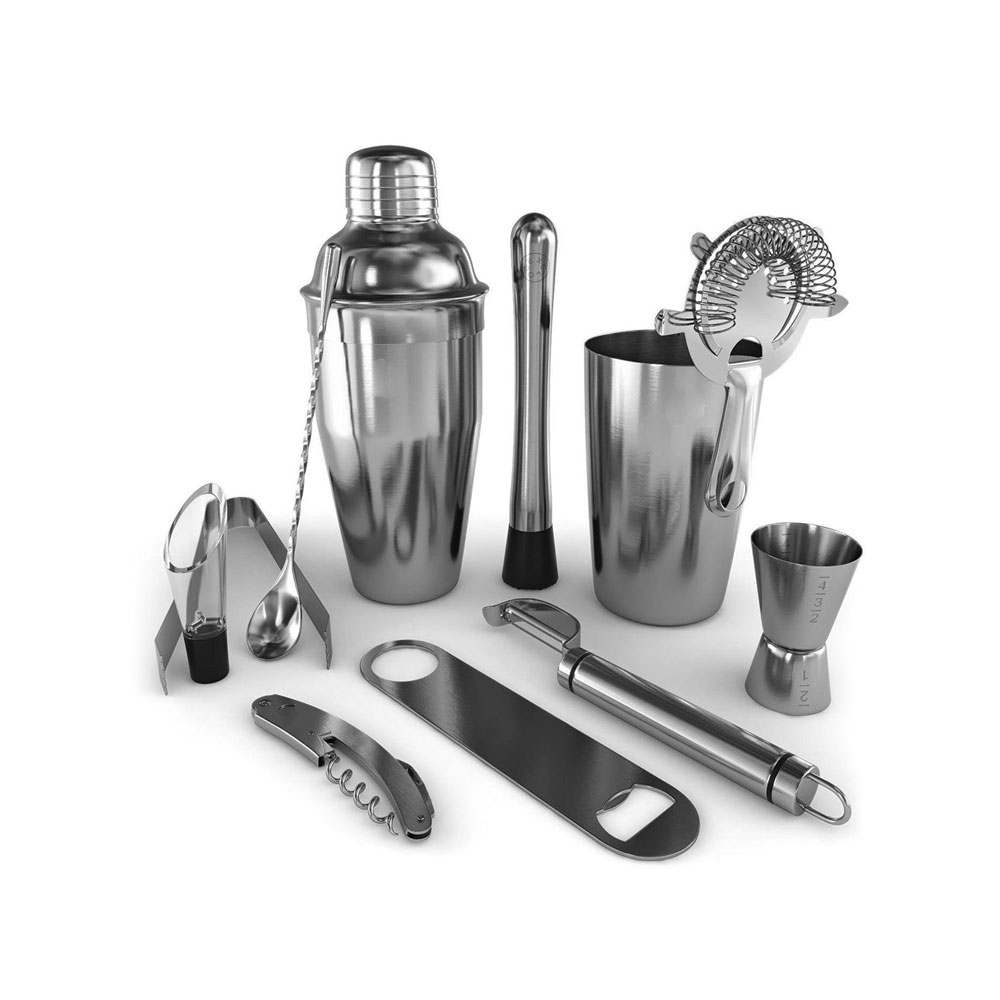