Why Stainless Steel?
Reasons for preferring stainless steels can be exemplified as corrosion resistance, resistance to high and low temperatures, strength, mechanical strength, ease of manufacturing, hygienic properties, appearance, and long service life.
- Corrosion Resistance: All stainless steels have high corrosion resistance. Low alloy types are resistant to atmospheric corrosion while high alloy types are resistant to environments even containing acids, alkaline solutions, and chlorides.
- High and Low Temperatures: In some types of stainless steel, the scaling and a significant decrease in the mechanical strength of the material are not observed even at high temperatures. Some types do not become brittle even at very low temperatures and thus, maintain their toughness.
- Strength: The carbon ratio of stainless steel can be increased for higher hardness and strength. The strength of the steel can be increased as desired by simply applying a low-temperature heat treatment after mechanical processing or manufacturing.
- Mechanical Strength: A great majority of stainless steel is hardened by cold forming, and thanks to the increase in strength, the material thicknesses in designs can be reduced, giving rise to significant reductions in weight and price. In some types, it is possible to give very high strength to the material by heat treatments.
- Ease of Manufacturing: Almost all stainless steel can be easily formed by cutting, welding, hot and cold forming, and machining processes.
- Hygienic Property: Stainless steels are easy to clean, which makes these materials widely used in hospitals, kitchens, food, and pharmaceutical industries.
- Appearance: Stainless steels are available in many different surface grades. The appearance, quality, and maintenance of these surfaces can be easily maintained for long periods.
- Long Service Life: Since stainless steels are durable and easy-to-maintain materials, they are economical material considering the entire service life of the produced part.
Austenitic
Since the corrosion resistance of austenitic stainless steels is higher than that of martensitic and ferritic stainless steels, they are more widely used. Any embrittlement below the temperature of transition from ductility to brittle, which is a very important problem seen in ferritic stainless steels due to the austenite internal structure, is not seen in such steels. Its corrosion resistance below zero (up to -270°C) and high temperatures and superior mechanical properties have enabled this steel group to be used as unrivaled structural steel in several areas.
AISI 304-grade austenitic steel is the most widely used stainless steel with its excellent formability, ductility, and adequate corrosion resistance. By adding molybdenum (Mo) to 304-grade steels, grades 316 and 317 are produced, and point corrosion resistance is ensured in controlled environments. Very low carbon steel grade 304L has been developed to prevent carbide precipitation, which occurs in the area under the heat effect during welding from steel grade 304, and leads to intergranular corrosion. High chromium alloys such as grade 309 and 310 are used in high alloys and oxidizing environments.
The share of austenitic steels in the total stainless-steel production is 70%, and grade 304 is the most commonly used grade among them.
It is the basic type of stainless steel. It provides high oxidation up to 400 °C. Its mechanical resistance and friction strength are very good.
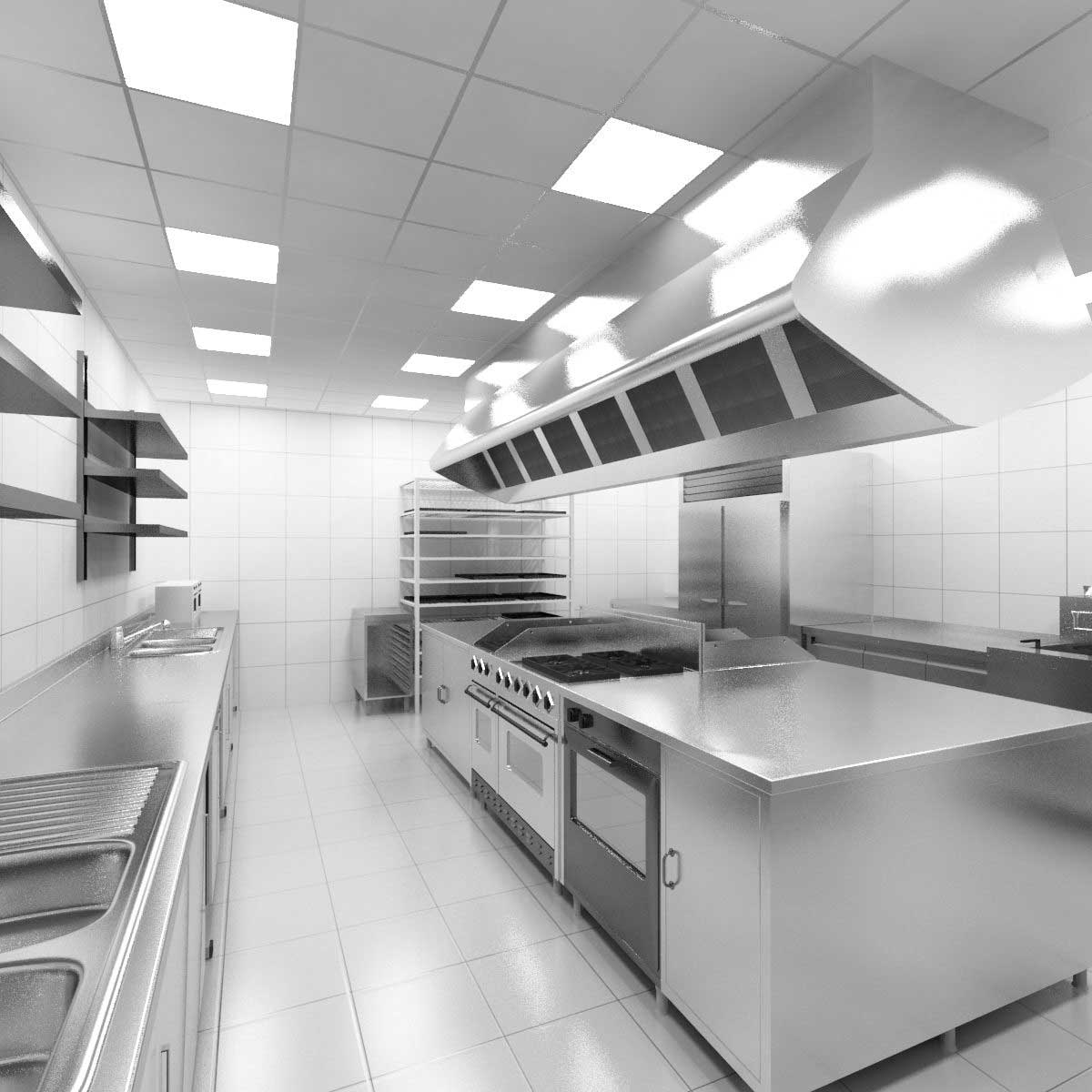
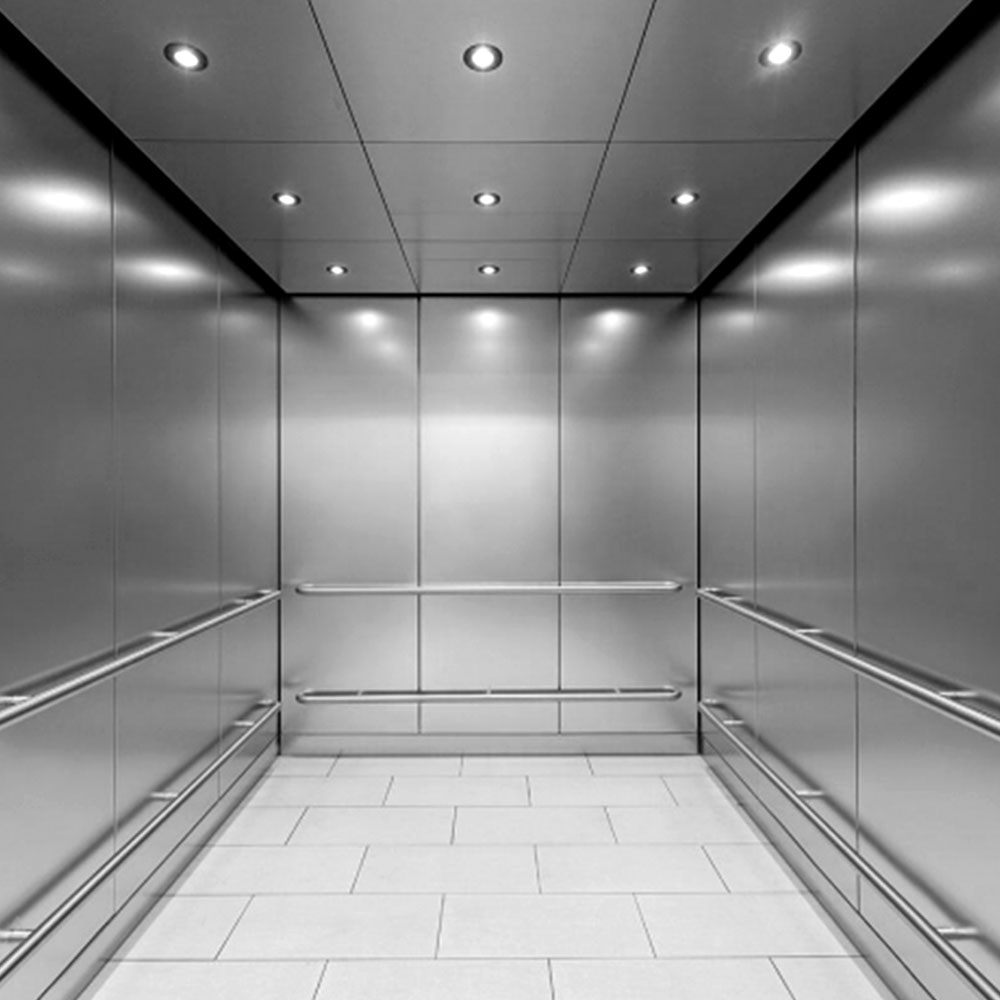
Ferritic
Ferritic is divided into 3 main groups according to their Chromium (Cr) ratio:
- The ones whose chromium content varies between 11-13%: (Grade 409, 410S, 1.4003 Grades) In the 1st group with low chromium content, it has moderate oxidation and corrosion resistance, low price, and good manufacturing properties. The most widely used one of this group, which is used in automotive exhaust parts, is grade 409.
- The ones whose chromium content varies between 14-18%: (Grade 430, 434, 436, 439, 430Ti, 441, 444) These are grades that contain moderate chromium and are used in the production of automotive parts and kitchenware, and have low impact resistance and weldability. Molybdenum (Mo) is added to some grades in this group to provide extra corrosion resistance.
- The ones whose chromium content varies between 19-30% (Super Ferritics): (grade 442 and 446) This group is examined separately from ferritic grades, and they are special grades. They are preferred where high corrosion and oxidation resistance are required.
Ferritic grades are more affordable than austenitic materials. For this reason, they are preferred in cases where this will not cause problems in the product and application if used. The magnetic quality of ferritic grades reduces their preferability compared to austenitic grades, but this disadvantage turns into an advantage in some application areas. An example of this is that the embedded refrigerator is magnetic.
Compared to carbon steel, the ferritic group has all the advantages of stainless steel, such as corrosion resistance, low total cost of life, longevity, aesthetic appeal.
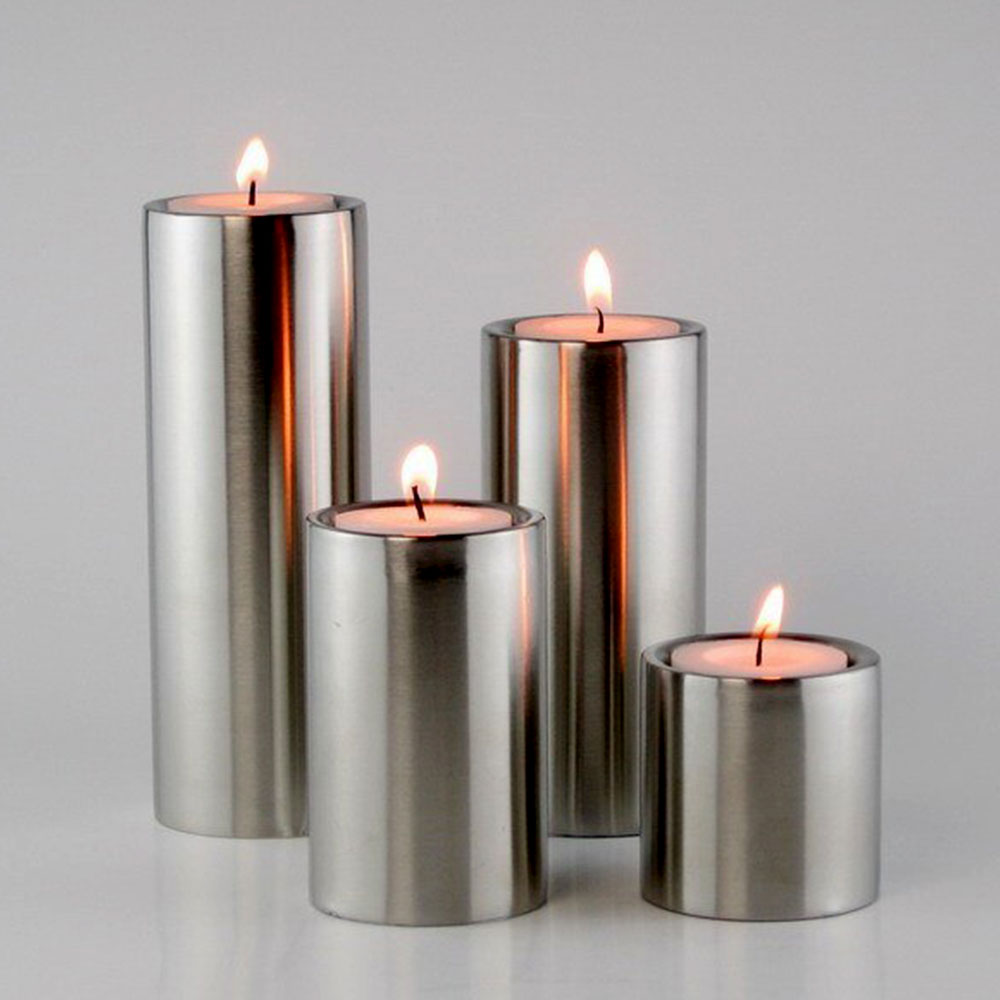
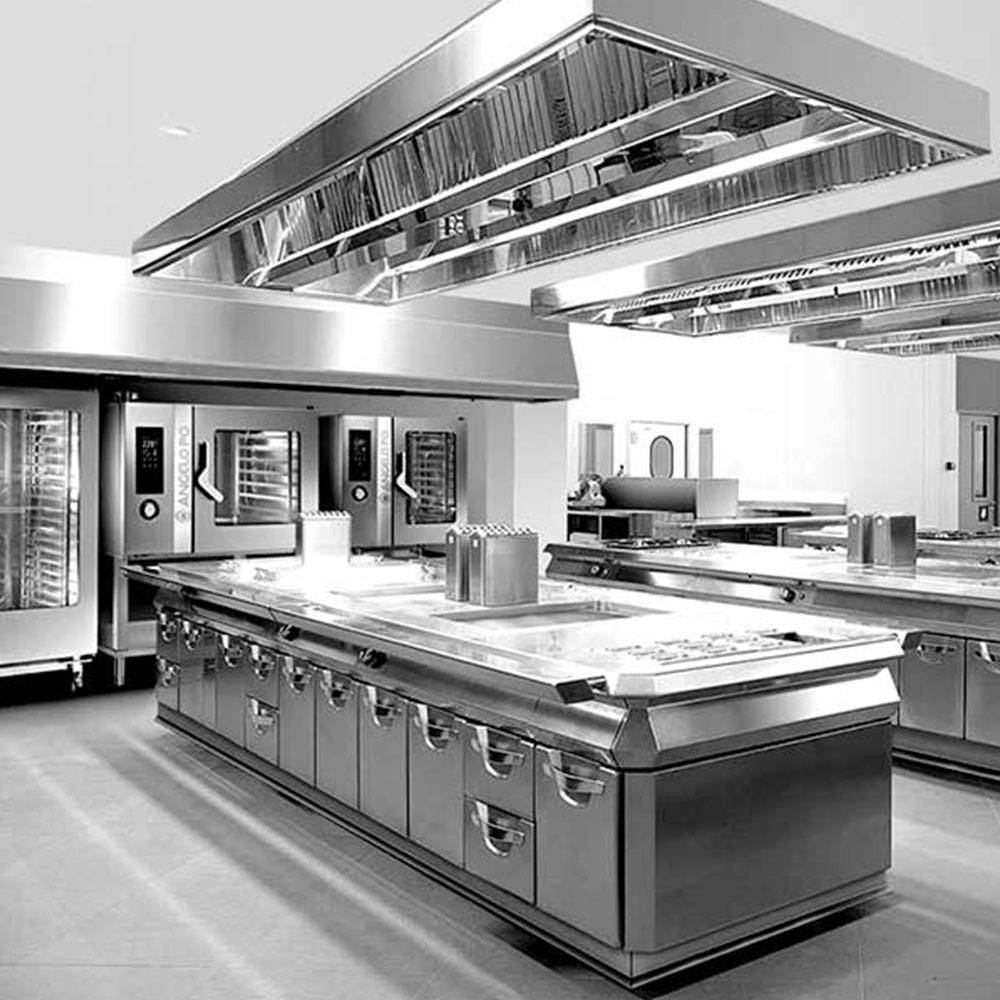
Duplex
In addition to the high properties of duplex stainless steels such as ductility, toughness, and corrosion resistance, the decrease in mechanical strength and corrugated corrosion resistance due to secondary phases arising from high thermal input restricts its usage areas and temperature of use for duplex stainless steels.
Although this stainless-steel grade is more costly per kilogram compared to other grades, it is a product that comes to the forefront in terms of price/performance as it can reach a high level of durability even in thinner materials. This grade, which is frequently used in areas requiring strength, flexibility, and durability, is used in pump shafts, boat shafts, propeller construction, special hydroelectric power plants, food industry, chemical industry, and machine production. Duplex stainless has a very high degree of mechanical strength and corrosion resistance as well as being flexible as austenitic stainless steel. For these reasons, it is recommended to use this grade of stainless-steel materials wherever quality, lightness, and durability are required.
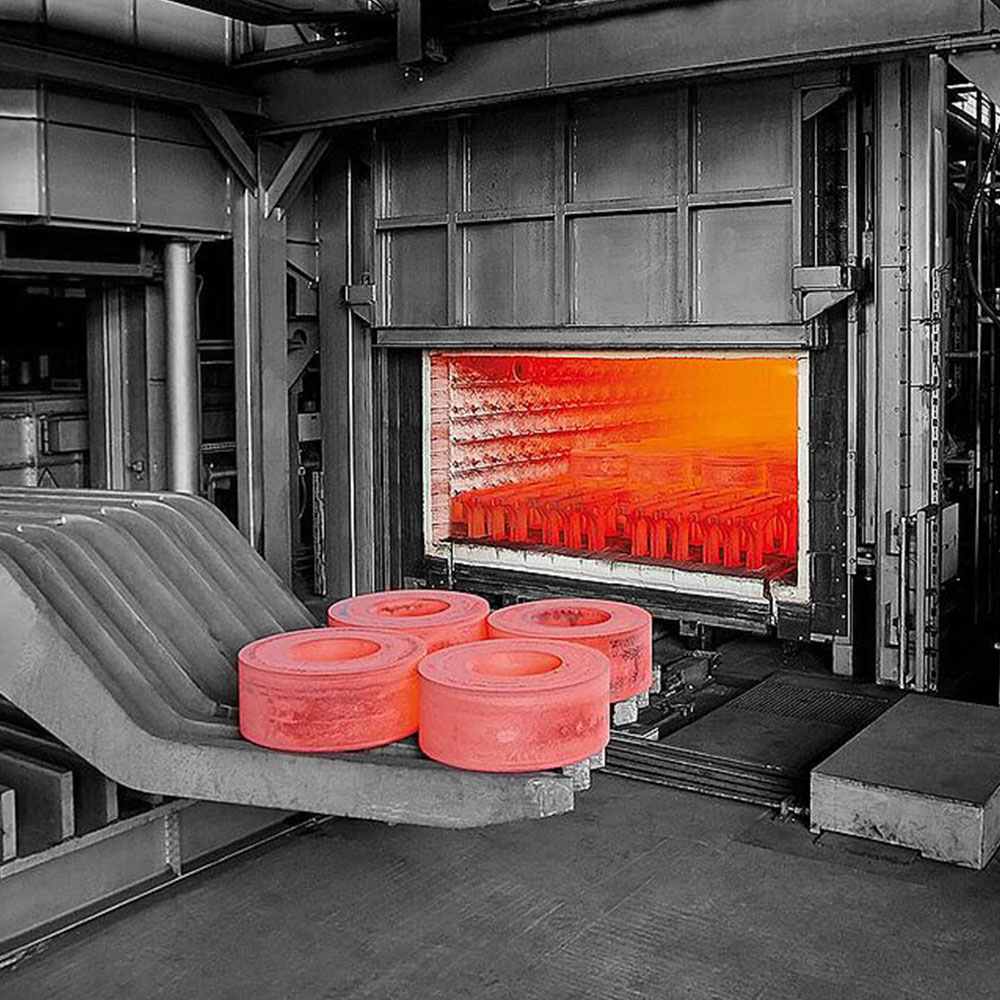
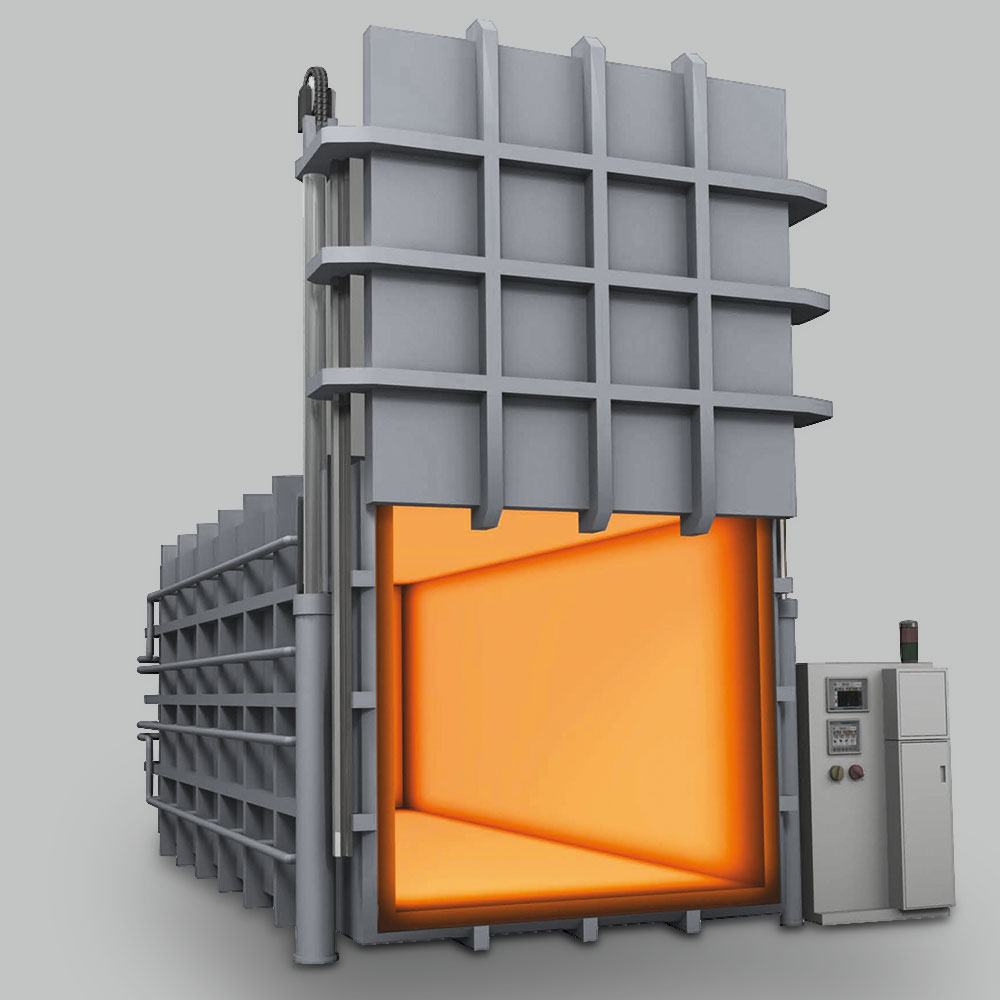
Martensitic
Martensitic stainless, being one of the steel types, is an alloy created for industries where durability and long service life are required. In this way, the products switch between products that can be used for a long time.
Since this type of steel has very good hardness, it is mostly used in sectors that require this property. This material is often used mostly in the knife sector and in surgical instruments that require durability. In this way, a very good advantage can be obtained with the help of the alloy, specifically in items where durability is most important.
Martensitic Structure is harder than others and it has a very good structure in terms of durability. However, it is also very fragile. It should be noted that its fragility level is higher than the others. Since excessive hardness will also cause brittleness, the hardness rate can be slightly reduced by the annealing method during manufacturing. Thus, the strength of martensitic stainless steel can be adjusted to the desired level.
On the other hand, it has a distinctive feature among other steel products. It has a structure that is slightly more susceptible to rust than others. These disadvantages can reveal specifically in long-term use.
It is used in piping heat exchangers and recuperators in petrochemical industries; steam and water valves, fittings, kitchen utensils, and sports equipment. It is used to make threaded pipes in carbon dioxide and contaminated oil wells.
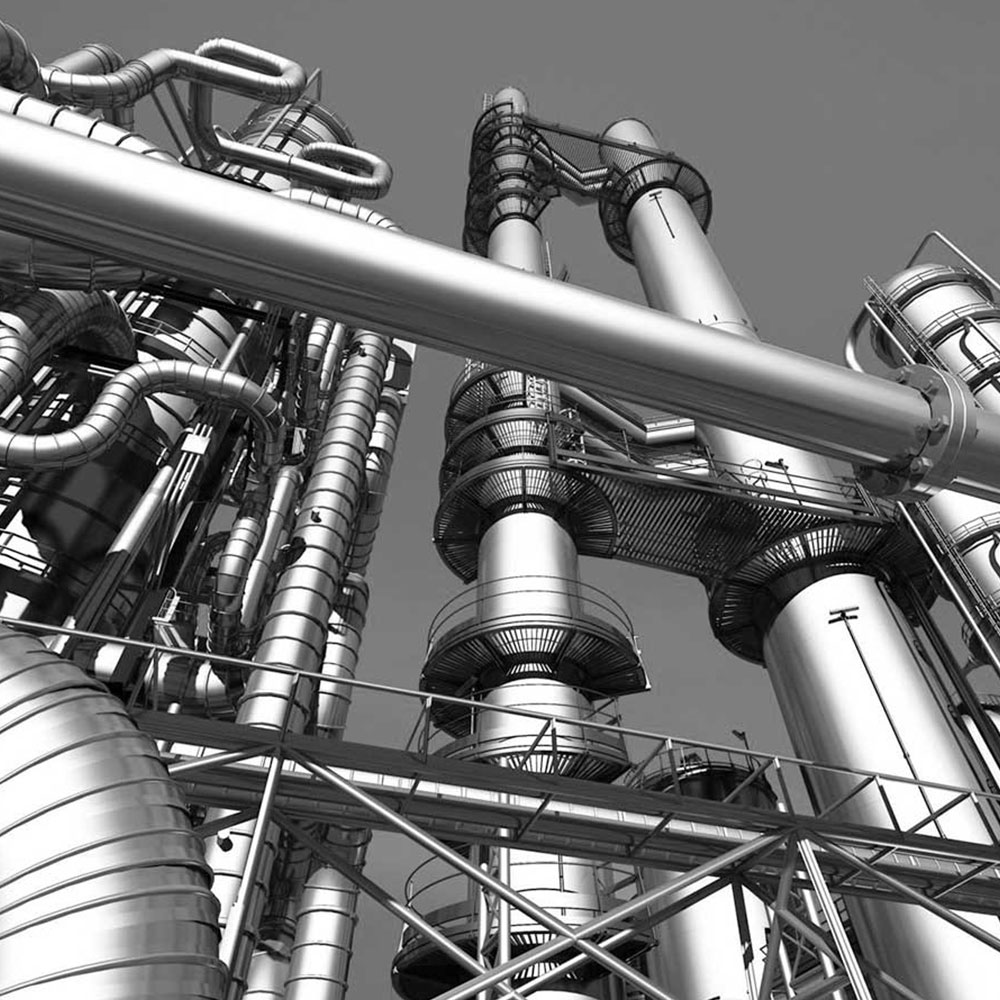
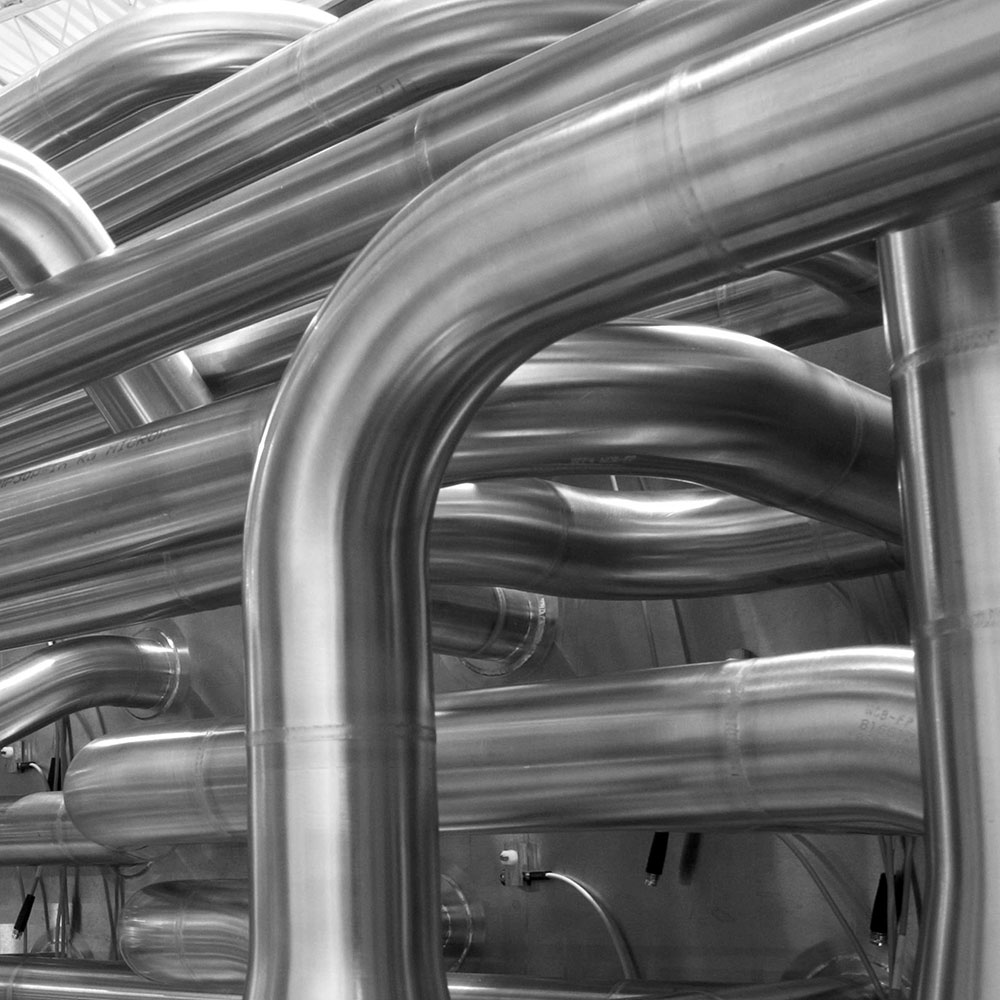